Examine This Report on Roar Solutions
Examine This Report on Roar Solutions
Blog Article
Examine This Report on Roar Solutions
Table of ContentsThe 8-Minute Rule for Roar SolutionsThe Basic Principles Of Roar Solutions The Main Principles Of Roar Solutions
In order to shield setups from a prospective surge a method of evaluating and categorizing a possibly hazardous location is required. The objective of this is to make certain the right selection and installment of equipment to inevitably avoid a surge and to make sure safety of life.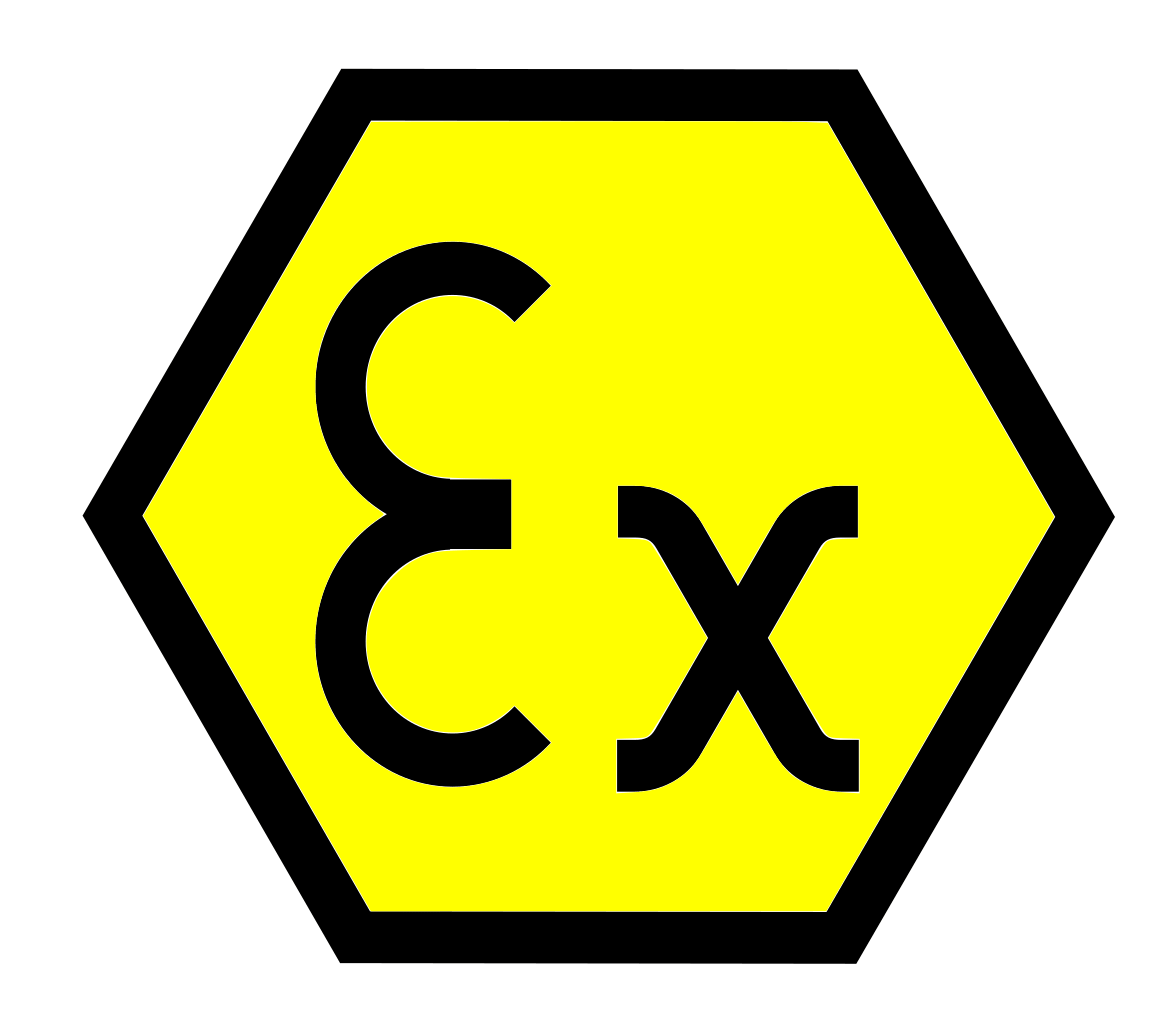
(https://www.reverbnation.com/roarsolutions)
No devices must be installed where the surface area temperature level of the equipment is greater than the ignition temperature of the given risk. Below are some common dust dangerous and their minimal ignition temperature level. Coal Dust 380C 225C Polythene 420C (thaws) Methyl Cellulose 420C 320C Starch 460C 435C Flour 490C 340C Sugar 490C 460C Grain Dirt 510C 300C Phenolic Material 530C > 450C Aluminium 590C > 450C PVC 700C > 450C Soot 810C 570C The probability of the threat being existing in a focus high sufficient to trigger an ignition will vary from place to place.
In order to identify this threat an installation is split right into locations of risk relying on the quantity of time the harmful exists. These locations are referred to as Areas. For gases and vapours and dirts and fibres there are 3 areas. Zone 0 Zone 20 A dangerous environment is highly most likely to be existing and may exist for long periods of time (> 1000 hours each year) or even continuously Area 1 Zone 21 A hazardous atmosphere is feasible but unlikely to be existing for extended periods of time (> 10 450 C [842 F] A category of T6 implies the minimal ignition temperature level is > 85 C [185 F] Unsafe area electrical equipment possibly designed for usage in higher ambient temperature levels. This would showed on the ranking plate e.g. EExe II C T3 Ta + 60C( This implies at 60C ambient T3 will not be gone beyond) T1 T1, T2, T3, T4, T5, T6 T2 T2, T3, T4, T5, T6 T3 T3, T4, T5, T6 T4 T4, T5, T6 T5 T5, T6 T6 T6 A T Class rating of T1 suggests the maximum surface temperature level created by the tool at 40 C is 450 C. Presuming the associated T Course and Temperature level score for the equipment are ideal for the area, you can constantly utilize a tool with a much more rigorous Division ranking than required for the location. There isn't a clear answer to this inquiry. It actually does depend upon the kind of devices and what repair services need to be lugged out. Tools with particular examination treatments that can't be carried out in the area in order to achieve/maintain 3rd party score. Have to come back to the manufacturing facility if it is prior to the devices's solution. Area Repair Work By Authorised Worker: Complicated testing might not be called for however certain treatments may need to be adhered to in order for the equipment to preserve its 3rd celebration ranking. Authorised employees have to be employed to do the job correctly Repair work should be a like for like substitute. New element need to be taken into consideration as a straight substitute needing no unique testing of the tools after the repair service is total. Each tool with an unsafe ranking should be evaluated individually. These are laid out at a high degree below, but for more detailed information, please refer straight to the standards.
Roar Solutions Things To Know Before You Get This
The equipment register is an extensive data source of equipment documents that consists of a minimum collection of areas to determine each thing's place, technical parameters, Ex-spouse classification, age, and ecological data. This information is important for monitoring and handling the equipment efficiently within hazardous areas. On the other hand, for periodic or RBI sampling examinations, the grade will certainly be a mix of In-depth and Close examinations. The proportion of Comprehensive to Shut inspections will be established by the Equipment Danger, which is analyzed based upon ignition risk (the possibility of a resource of ignition versus the chance of a flammable environment )and the harmful area classification
( Zone 0, 1, or 2). This variation will certainly additionally influence the resourcing demands for job prep work. When Whole lots are specified, you can establish tasting strategies based upon the sample dimension of each Great deal, which describes the variety of random equipment things to be evaluated. To identify the called for sample dimension, 2 aspects need to be evaluated: the size of the Lot and the category of inspection, which indicates the level of effort that should be applied( decreased, typical, or enhanced )to the assessment of the Whole lot. By incorporating the group of examination with the Whole lot dimension, you can after that develop the ideal denial standards for a sample, meaning the permitted number of faulty things discovered within that sample. For even more details on this process, please refer to the Power Institute Standards. The IEC 60079 typical advises that the optimum interval in between assessments should not go beyond 3 years. EEHA evaluations will additionally be performed outside of RBI projects as component of scheduled maintenance and equipment overhauls or repair work. These inspections can be attributed toward the RBI example dimensions within the impacted Whole lots. EEHA assessments are carried out to recognize faults in electric devices. A heavy racking up system is vital, as a single item of equipment might have multiple mistakes, each with varying degrees of ignition risk. If the mixed rating of both inspections is much less than twice the mistake rating, the Great deal is deemed appropriate. If the Whole lot is still taken into consideration undesirable, it needs to undergo a complete evaluation or validation, which may cause stricter examination procedures. Accepted Whole lot: The reasons for any kind of faults are recognized. If a typical failure setting is found, extra tools may need evaluation and repair. Faults are classified by seriousness( Safety and security, Integrity, Home cleaning ), making sure that immediate issues are examined and addressed immediately to reduce any kind of effect on security or procedures. The EEHA data source ought to track and tape the lifecycle of faults in addition to the corrective actions taken. Executing a durable Risk-Based Evaluation( RBI )approach is vital for making sure compliance and safety and security in handling Electrical Tools in Hazardous Areas( EEHA) (hazardous area electrical course). Automated Mistake Scoring and Lifecycle Administration: Easily take care of mistakes and track their lifecycle to enhance evaluation precision. The intro of this assistance for risk-based examination further strengthens Inspectivity's position as a best-in-class remedy for governing compliance, as well as for any type of asset-centric examination usage instance. If you want discovering more, we welcome you to ask for a presentation and discover just how our solution can change your EEHA monitoring procedures.
Unknown Facts About Roar Solutions

In terms of explosive danger, an unsafe area is an environment in which an eruptive atmosphere exists (or might be expected to be present) in quantities that require unique precautions for the building and construction, setup and usage of devices. Roar Solutions. In this short article we explore the difficulties faced in the work environment, the threat control steps, and the called for proficiencies to function safely
It is a repercussion of modern life that we make, save or manage a variety of gases or fluids that are regarded flammable, and an array of dusts that are regarded combustible. These compounds can, in particular conditions, develop explosive environments and these can have major and heartbreaking consequences. The majority of us are acquainted with the fire triangle get rid of any one of the 3 aspects and the fire can not take place, yet what does this mean in the context of harmful areas? When damaging this see this here down right into its simplest terms it is essentially: a mix of a particular amount of launch or leak of a specific material or material, blending with ambient oxygen, and the visibility of a resource of ignition.
In the majority of circumstances, we can do little concerning the degrees of oxygen in the air, but we can have significant influence on resources of ignition, for instance electrical tools. Hazardous areas are recorded on the unsafe area classification drawing and are determined on-site by the triangular "EX" indication. Here, amongst other crucial info, zones are split right into 3 kinds depending upon the danger, the chance and period that an explosive atmosphere will exist; Area 0 or 20 is regarded one of the most unsafe and Area 2 or 22 is considered the least.
Report this page